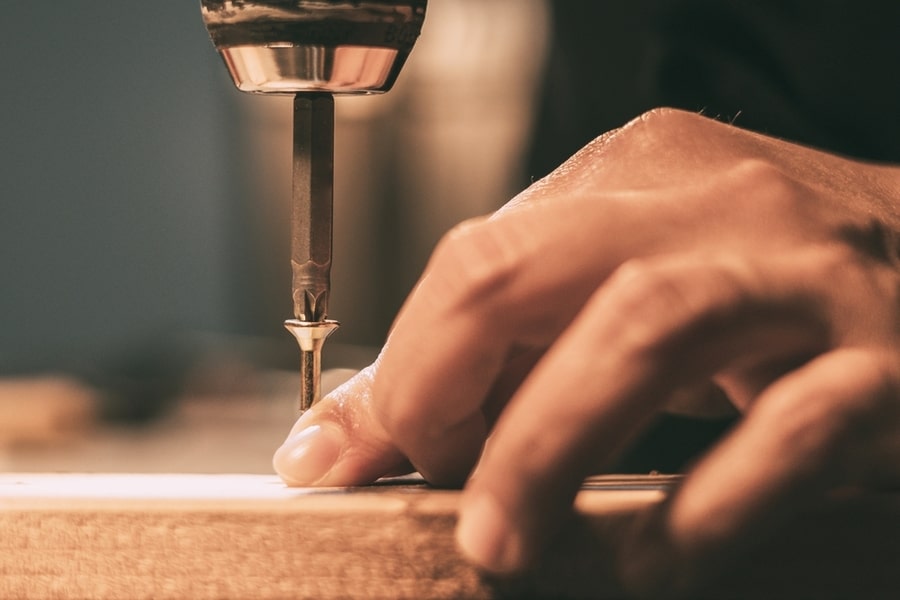
With their lithium-ion batteries, today’s cordless drills are more powerful than ever. While that extra power can be helpful, it can also cause a dreaded stripped screw. This guide minimizes your chances of stripping a screw with a drill.
You can do several things to ensure you don’t strip a screw. Follow proper drilling techniques to keep those screws from stripping.
- Drill a pilot hole
- Use a new driver bit
- Countersink your pilot hole
- Maintain correct pressure on your drill
- Change the screw head type
- Drill at a right angle
- Use an impact driver
- Use the correct driver bit
- Use a hand screwdriver
Did you already strip a screw or break the head off a screw? Don’t worry; this guide covers that, too.
Stripped screws are a nuisance. They are an eyesore; once stripped, they are difficult to unfasten. Read on to learn tricks that will help you avoid stripping.
Don’t Let Your Screw Strip
1. Drill a Pilot Hole
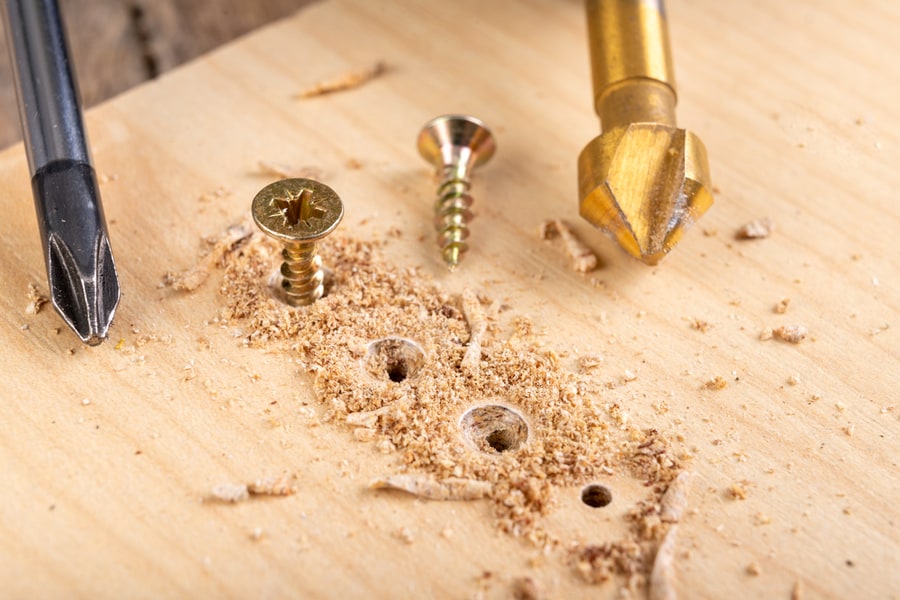
This is the most important way to avoid stripping your screws. Use a pilot bit to drill a hole for your screw to go into.
Drill It Like a Pro
Pilot holes are essential if you are drilling into hardwood. They are highly recommended when drilling into all other materials.
- The pilot hole should be the same size or slightly smaller as the screw shaft, not the screw threads.
- Set the depth of the pilot bit in your drill to match the length of the screw you are driving. So, if you’re using a 2″ screw, the drill bit should extend from your drill by 2″. Setting the depth just shorter than the screw is acceptable, too.
- Pro hack: Wrap some blue tape around your pilot bit at the depth you want to drill your hole. Release the drill trigger once the material being drilled reaches the blue tape. Check the tape often for slippage.
- If you’ve drilled a pilot hole and the screws are still stripping, you may need to increase the size of your pilot bit.
Drilling a pilot hole is the best way to avoid stripped screws.
2. Use a New Driver Bit
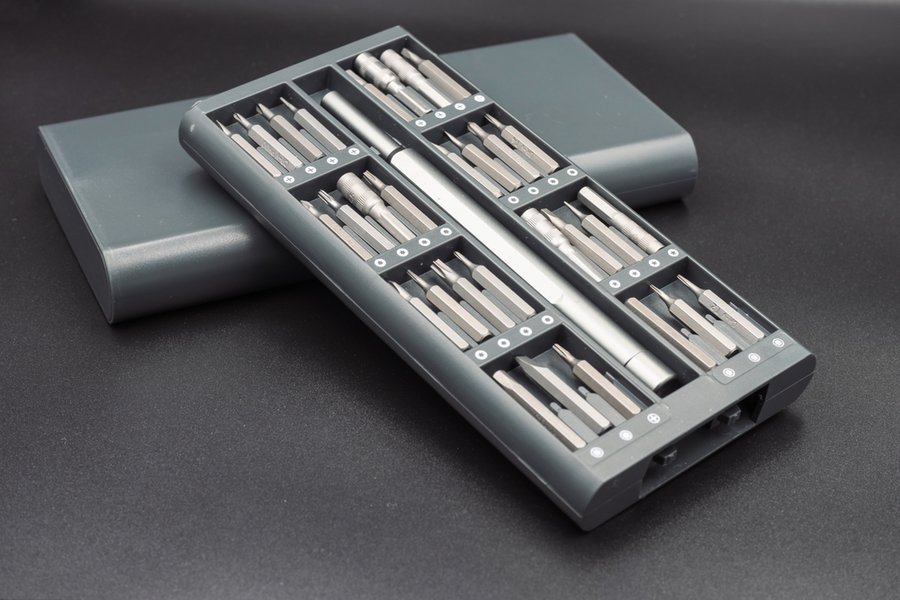
Over time, driver bits can wear down. Their fit to the screw head becomes poorer as they wear down, causing slippage. Once the driver bit begins slipping on the screw head, stripping starts.
Check your driver bits. Discard old driver bits and replace them with new ones.
3. Countersink Your Pilot Holes
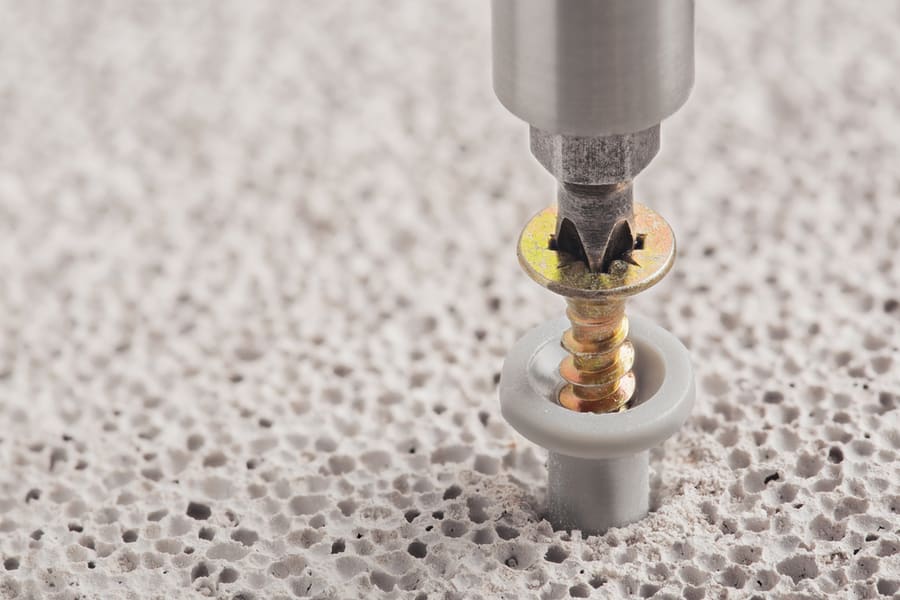
Once again, this is especially true for hardwood.
Only countersink material if you are using flathead screws.
If you attempt to recess the screw head into wood or other material and fail to countersink, the screw head may snap off. This outcome is suboptimal.
How To Remove a Stripped Screw
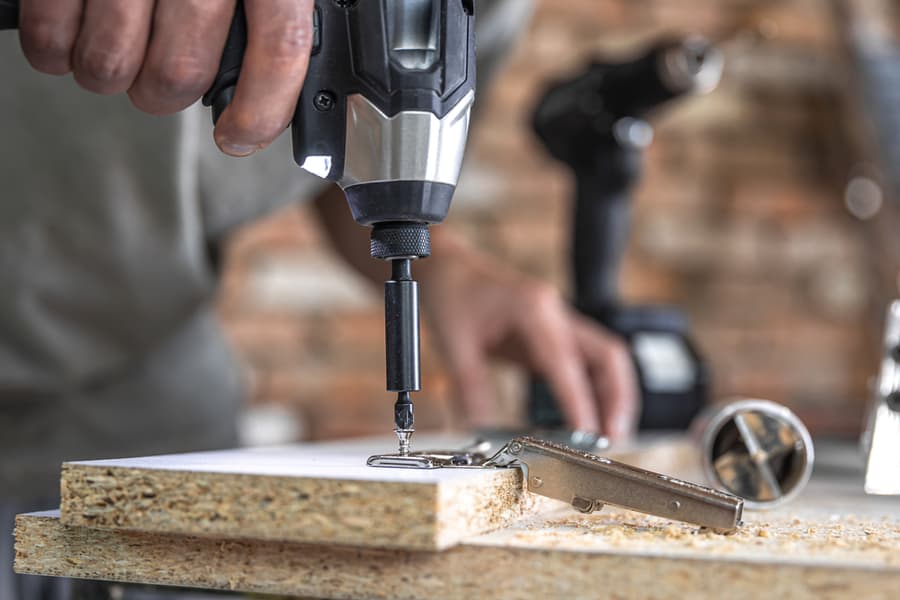
Oh no. My screw head snapped off. Or my screw is stripped. Now what?
Fear not. Follow these instructions to remove a screw that has become stripped.
- Using a channel lock or other pliers, grab the screw head or shank firmly and rotate counterclockwise. Continue rotating until the screw is removed.
- Is your screw still stuck? Try spraying lubricant onto the screw shank and into the screw hole.
- Saw the screw off with a reciprocating saw, oscillating saw, or hacksaw.
- If the head snapped off, the shank of the screw could be drilled out with a pilot bit.
Good work. You’ve successfully removed the stripped screw.
4. Maintain Pressure on Your Drill
You’re looking for the “Goldilocks zone” of pressure. Pushing too hard will make the drill slip off the screw (known as “cam out”), and you risk gouging into whatever you’re drilling.
Pushing too softly will cause the screw to release from the driver, leading to a stripped screw. Try to apply consistent, firm pressure.
5. Try a Different Screw Head Type
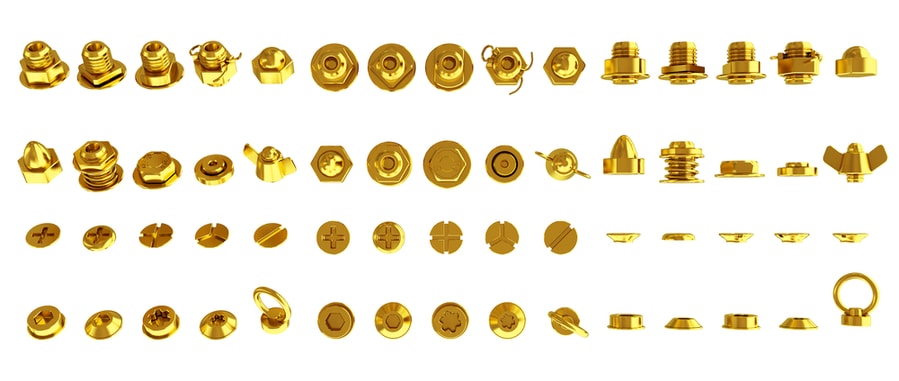
#2 Phillips screws are the most common type of screw head. They’re also more prone to come out than other screw heads.
Buy screws with a square or star head and use the appropriate driver. See if this helps you avoid stripping screws.
6. Drill at a Right-Angle
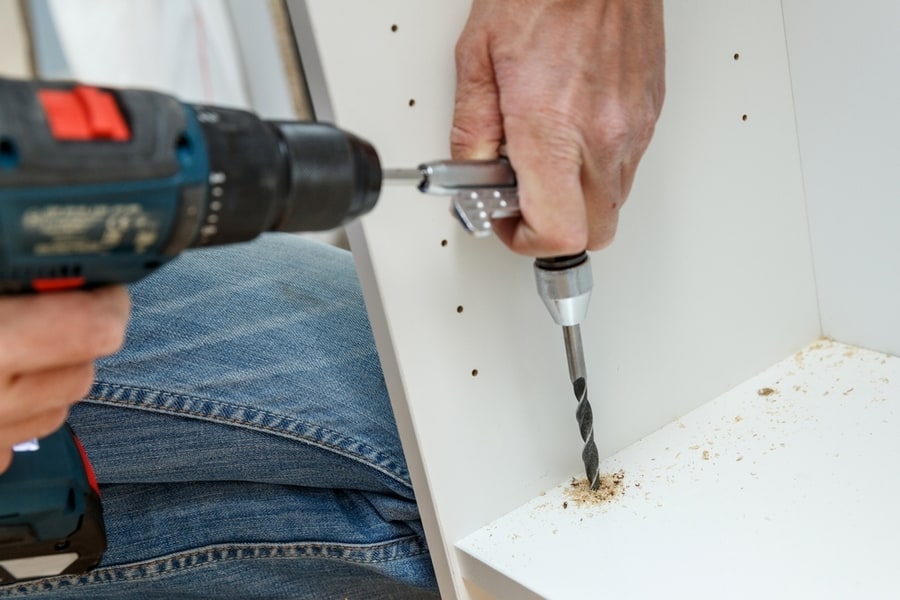
Your drill should be held at a 90-degree angle to whatever you fasten.
Check and make sure that your drill is angled properly. Even holding the drill off by a few degrees will cause cam out.
7. Get an Impact Driver

These types of drills are superior at driving screws. It’s right there in the name, impact driver.
Give one a try and see if it solves your problems.
8. Use the Correct Driver Bit
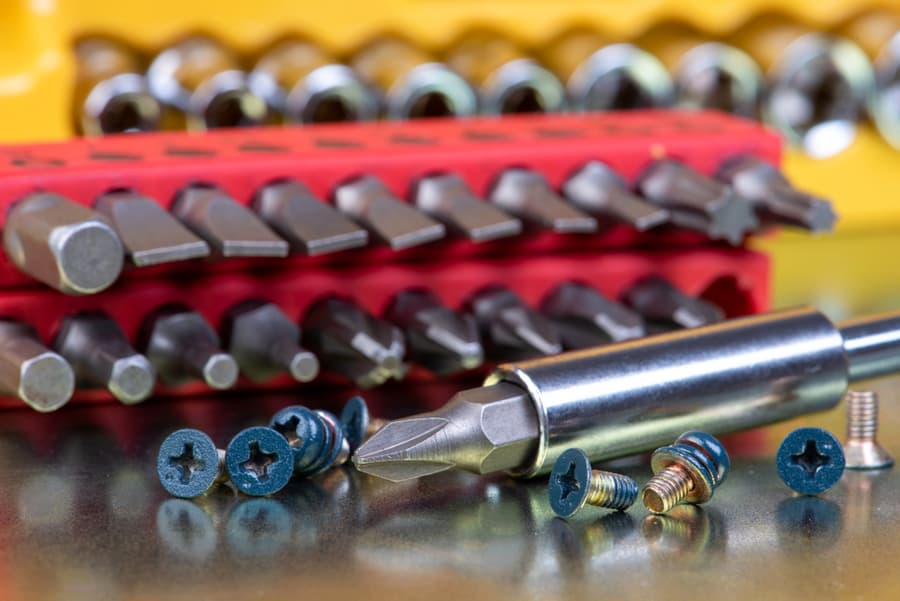
If you are using a T25 screw, it’s important to use a T25 driver. A T20 drill bit might look similar, but it is too small for a T25 screw.
If you try it, you’ll end up stripping the screw or wrecking the driver bit.
The same goes for Phillips drivers. There are PH1, PH2, and PH3 bits.
Knowing this distinction and pairing the correct screw head to the correct driver bit will keep screws from stripping.
9. Use a Hand Screwdriver
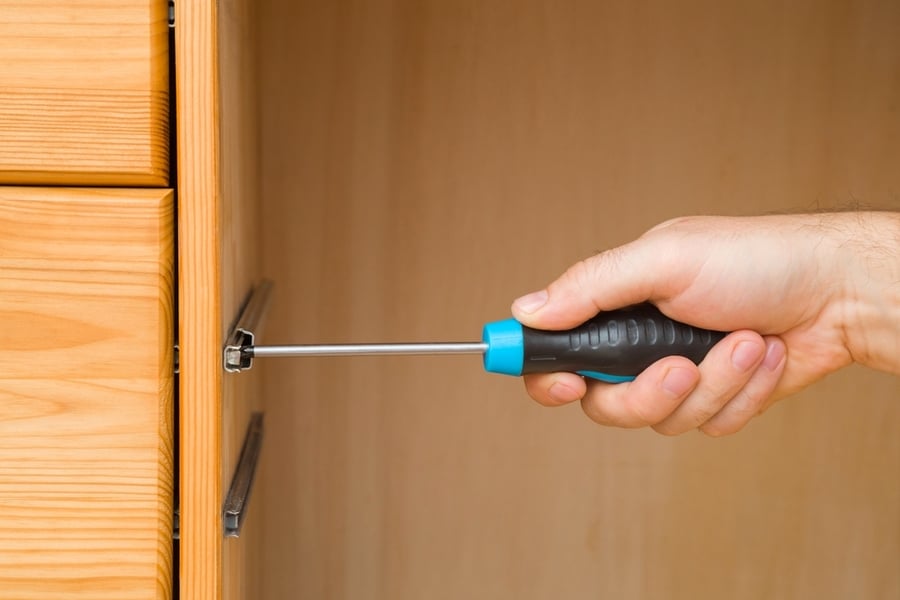
I know that power tools are more fun. And faster and easier. But sometimes, you need to go old school.
If the screw you are using is slotted, a hand screwdriver is your best choice. Drills tend to wander and slip off slotted screws.
There isn’t enough there for the driver to grab onto. So put your drill back in its pouch and grab a hand screwdriver.
Don’t Strip Your Screws
There are several reasons your screws might be getting stripped. Drilling a pilot hole is the best way to prevent stripping. Other best practices include ensuring your driver bit is new, countersinking pilot holes, and maintaining pressure on your drill.
Trying out different types of screw heads, holding your drill at a 90-degree angle, and using an impact driver are other ways to avoid stripping screws.
Also, make sure you’re using the correct driver bit. And when all else fails, give an old-fashioned hand screwdriver a try.
Don’t panic if your screw is stripped. Relax, grab some channel locks, and rotate the screw out counterclockwise.