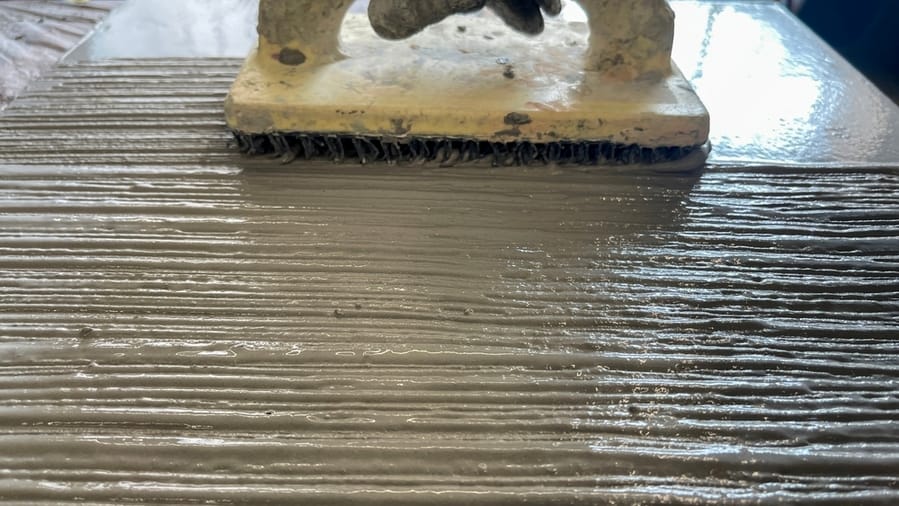
Concrete is a structural material that provides strength, versatility, and durability during construction. It comes in different classes or grades to denote the structure’s stability.
One new type of concrete growing in popularity is Ultra-High-Performance concrete (UHPC). It is well-known for its outstanding strength and durability. But how is Ultra-High-Performance concrete made?
Making Ultra-High-Performance concrete is easy, provided you know the ingredients and proportions. Often you will need to mix the following ingredients to make UHPC:
- Dry mix cement, silica fume, fine sand, and coarse sand.
- Add water and HRWR and mix.
- Finally, add steel fiber and mix.
If necessary, add a defoaming agent of at least 0.5 lb per cubic yard to reduce the bubbles during vigorous mixing.
In this article, you’ll learn how to make Ultra-High-Performance concrete.
Step-by-Step Guide on How To Make Ultra-High-Performance Concrete?
Ultra-High-Performance concrete is used worldwide because of its better performance than regular concrete. The minimum compressive force of UHPC is 120 MPa or 17000 pounds per square inch.
It is often used in large products like bridges, but you can use it for small-scale projects that require more durability, like pouring a concrete foundation for a home.
The trick to successfully mixing UHPC depends on the type of high-range water reducer you use and the carbon content of the silica fume. Carbon particles in the silica fumes are fine, which can increase water demand, thus causing mixing problems.
Below we elaborate on the steps to take on how to mix a cubic yard of UHPC with ease:
Step #1: Determine How Much Concrete You Need
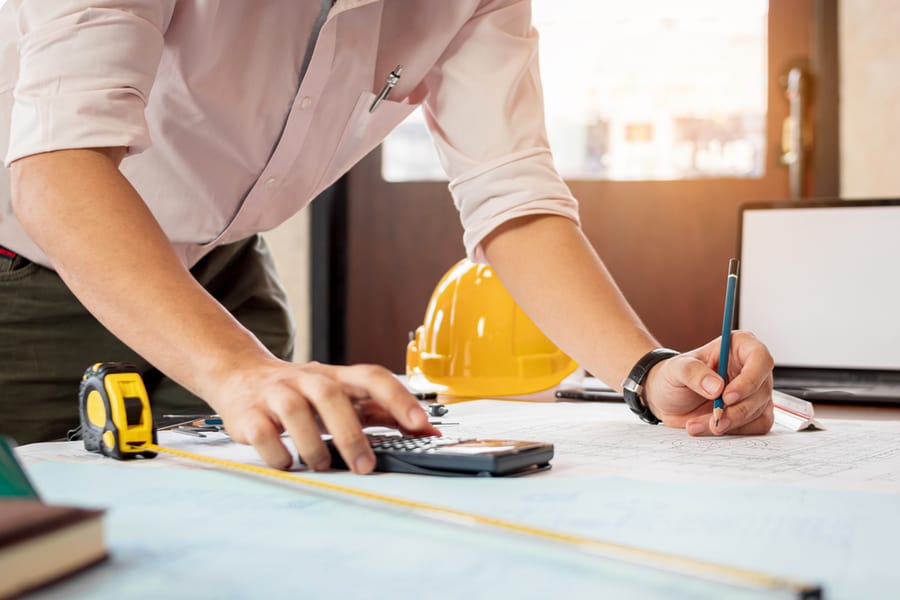
The first thing you want to do is to determine the amount of concrete you need for the job. To achieve this, calculate the areas by measuring the length and width of the surface you want to cover.
Also, determine how thick you want the concrete to be. Based on these figures, you can input them into a concrete calculator to know how much concrete is required to complete the project.
Step #2: Get a Suitable Concrete Material
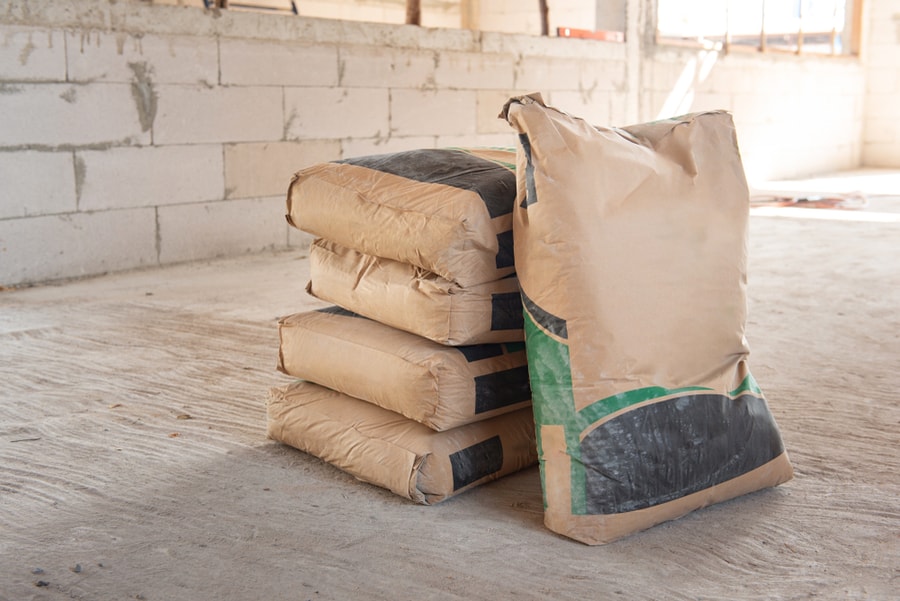
Next, you want to get suitable materials for the UHPC. For example, Type I portland cement is one of the main ingredients in a UHPC mix.
If you can’t access Portland cement in your area, use other cementitious materials like fly ash or slag cement. You will also need SIlica fume, silicon sand (fine and coarse), steel fiber, high-range water reducer (HRWR), defoaming agents, and water.
Step #3: Determine How Much Coarse and Fine Aggregate You Need
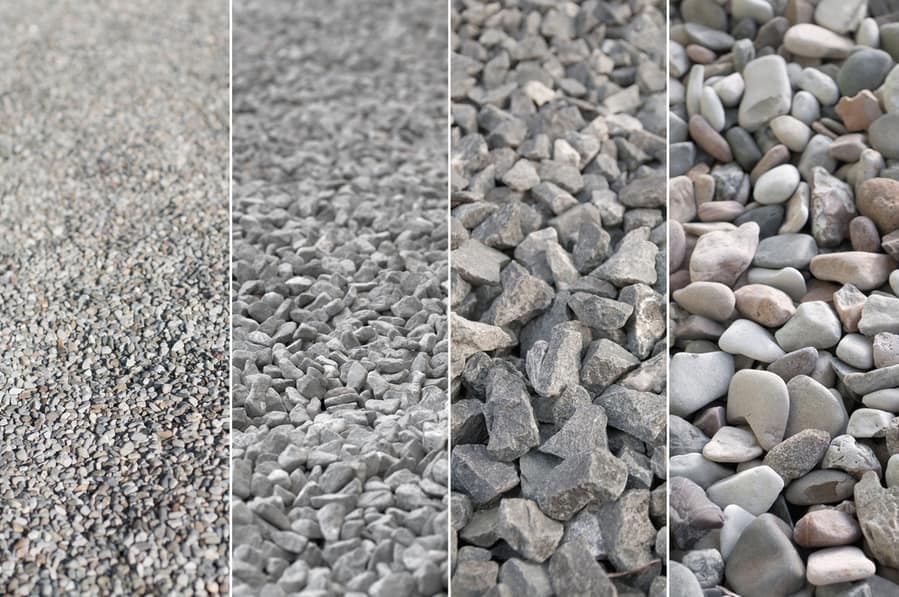
When making UHPC, there must be a delicate balance between the ingredients you use—mainly in the coarse and fine aggregate ratio. The standard ratio is to mix 11% cement with 26% fine aggregate and 41% coarse aggregate.
The remaining 22% is accounted for in air and liquid totals.
Step #4: Mix Coarse Aggregate With Silica Fume
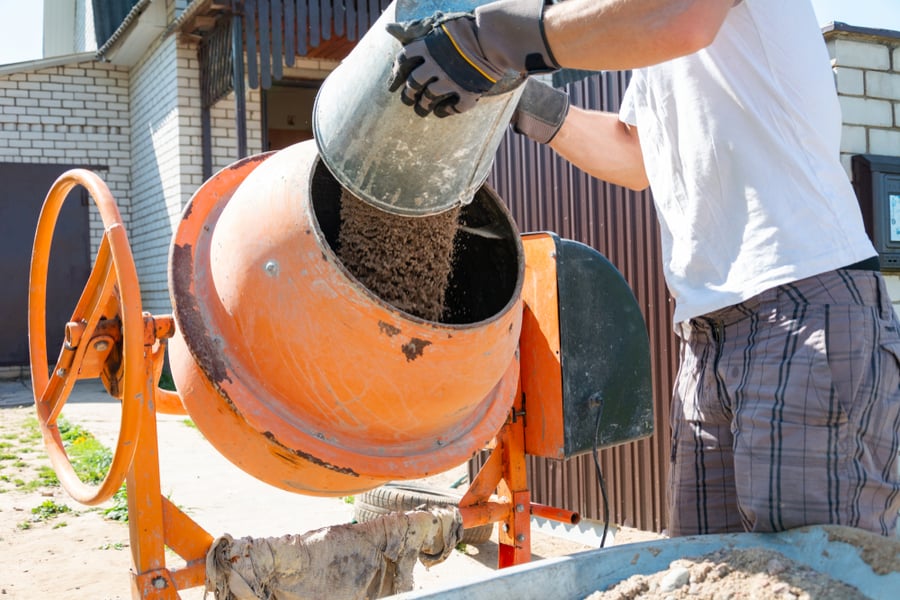
With all the material at hand, start mixing the dry material first. Next, pour about 1580 lb of coarse sand into a cement mixer. The coarse sand should have a grain size between 400 and 800 microns.
Turn on the mixer, and slowly add about 327 lb of silica fume. You should mix these dry ingredients for about 2 to 5 minutes.
Step #5: Add Cement to the Mix
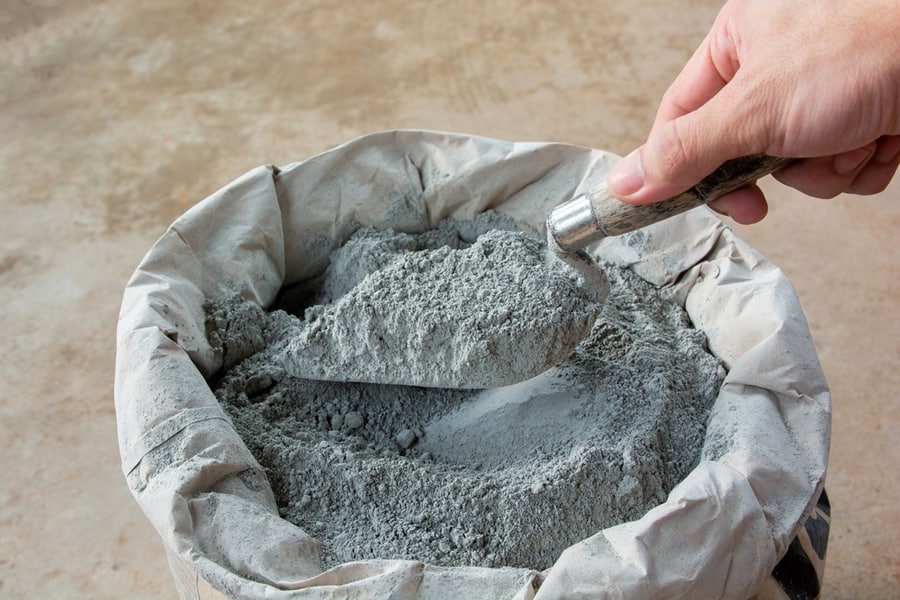
While the coarse aggregate mixture spins in the mixer, add the cement. You will need about 653 lb of Type I Poland Cement to make UHPC. When you add the cement, mix for 3 to 5 minutes until all the dry materials are combined. The cement will not be activated until you add water to the mix.
Step #6: Add the Fine Aggregate
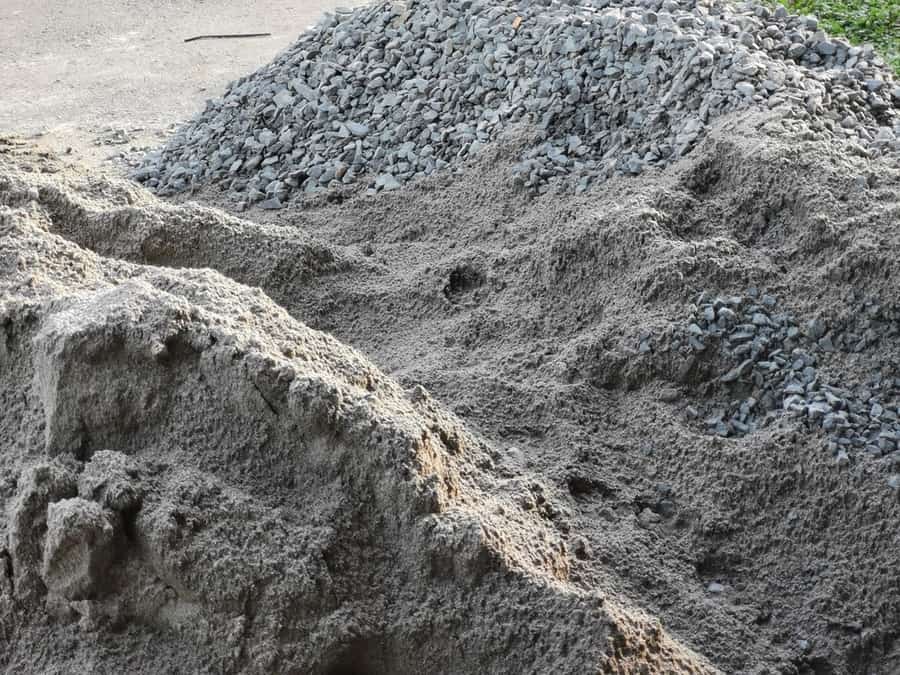
Add the fine aggregates into the cement mixer and keep mixing. You will need about 395 lb of fine sand. The fine sand should have a grain size of 80 to 200 microns.
Step #7: Add Water to the Mixture
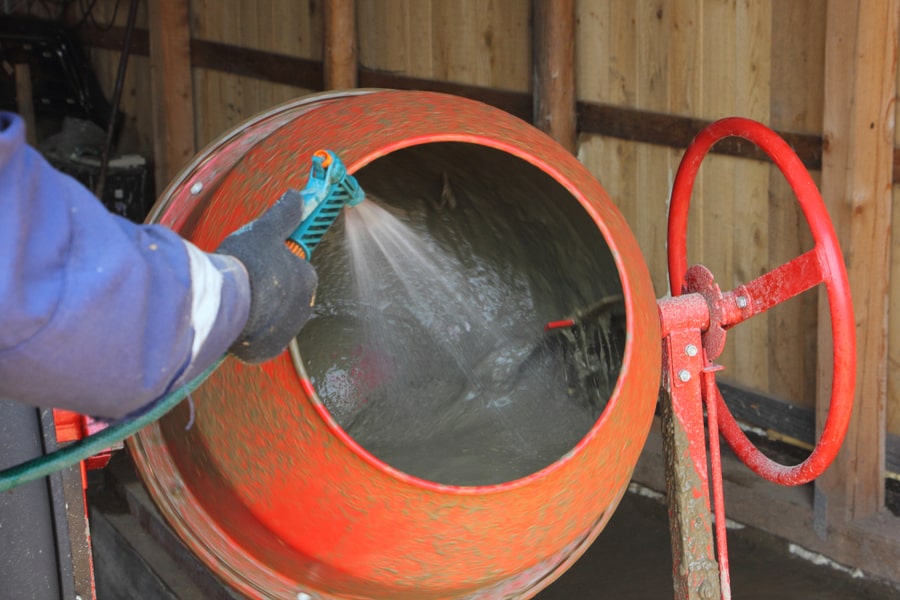
Add the water to the mixture at this stage and mix for about 2 minutes. You will need about 31.6 gallons of water to add gradually to the mix.
Also, add about 550 oz of HRWR for this mix. Finally, mix 2% of steel fibers, about 265 lbs, to achieve fluidity.
Step #8: Mix Properly
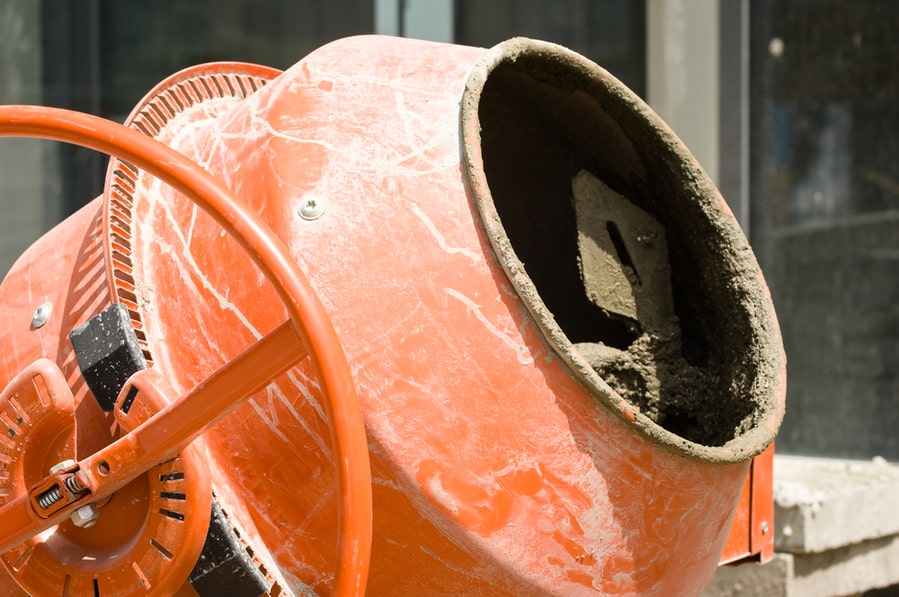
As you mix the formulated UHPC, it may form bubbles. To curb excessive bubbles, add about 0.5 lb of a deforming agent. Mix the concrete for 15 more minutes after adding the final ingredient before casting.
When you cast the concrete, note that it may take seven days or more to cure correctly. During those seven days, you must use two days for hot water curing to prevent cracks.
What Are the Qualities of Ultra-High-Performance Concrete?
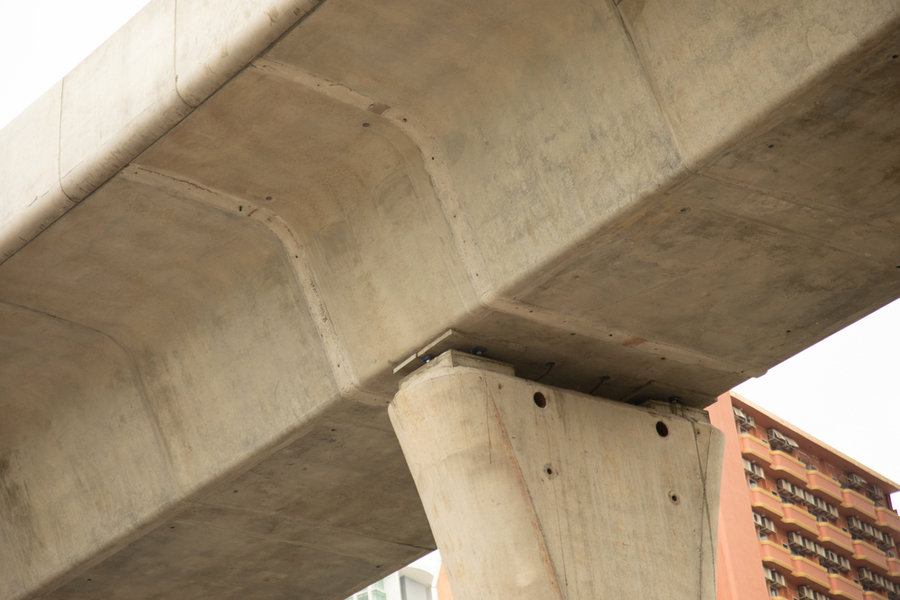
UHPC is an excellent building material with a projected lifespan of over 100 years. Some of the qualities of UHPC that make it so exceptional include the following:
1. Durability
The durability of UHPC exceeds exceptionally. Ideally, durability measures a material’s performance under extreme conditions, of which UHPC performs excellently.
When it comes to freezing and thawing resistance, the UHPC still exhibits 100% of its properties even after 600 cycles of freezing and thawing.
In terms of chloride permeability which is the cause of most concrete failing, UHPC being subjected to 3% sodium chloride solution for 90 days only shows less than 10% of permeability. And regarding abrasion resistance, UHPC is about twice as resistant as regular concrete.
Generally, UHPC has properties that are similar to hard rock.
2. Strength
When it comes to the strength of concrete, compression, load-bearing capacity, and tension strength come to mind. UHPC has a high compressive strength to resist bending under a load.
The compressive strength of regular concrete is between 3000 and 5000 psi, whereas the compressive strength of UHPC is between 18000 and 35000 psi.
Aside from its impressive compressive strength, UHPC has a tensile strength twice that of regular concrete. The tensile strength tells how much the concrete can resist being pulled.
The tensile strength of normal concrete is between 400 and 700 psi, whereas the tensile strength of UHPC is around 1400 psi.
Conclusion
In conclusion, UHPC’s unique material combination of superior properties has facilitated builders’ ability to create attractive yet durable structures that can stand the test of time.
Making UHPC is easy, as you can see from this guide. All you need are suitable materials and the ideal proportion.
Once you have that, you can enjoy the many unique advantages UHPC offers, such as construction speed, superior durability, impermeability against impact, abrasion, corrosion, and so on, which reduce maintenance and prolong lifespan.
Frequently Asked Questions
What Is the Best Curing Condition for Ultra-High-Performance Concrete?
Treat the UHPC with heat for 48 hours after demolding it to achieve the desired strength. Also, the curing conditions are a temperature of 195 F or 90 C and a relative humidity of 95%.
If the conditions are harsh, there is a high chance of visible cracks on the concrete.
How To Know if You Have the Right Consistency for Ultra-High-Performance Concrete?
The best way to tell if the consistency of a UHPC is correct is to perform a spread test. After mixing the paste, place the fresh mix in a spreading cone.
The UHPC is used to fill the cone to the rim and then lifted at a fixed pace. Due to the high flowability of the concrete, you don’t need to compact or vibrate the cone to achieve the desired result.
So, what is left at the base is left to spread for 2 minutes. Then, the perpendicular direction of the average diameter of the spread is measured.
The good spread for the right consistency of UHPC should be between 175 mm and 300 mm.